With Bette in the bathroom: first 3D printed home in Germany
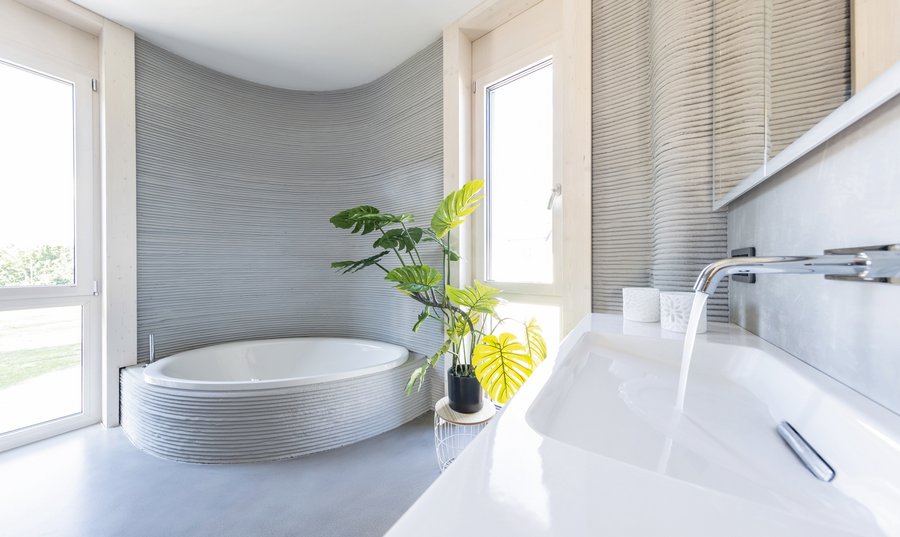
For
planner and architect Alexander Hoffmann 3D printing also means a high degree of
design freedom in the design of bathrooms.
Photo: Peri GmbH
Beckum in
Münsterland is now home to Germany's first single-family house built using the
3D concrete printing process. The visionary project features a Bette bath tub
and two Bette shower trays.
For
planner and architect Alexander Hoffmann from Mense-Korte ingenieure +
architekten, who supervised the project, 3D printing means a high degree of
design freedom in the design of buildings. If the technology catches on,
Hoffmann says, they will be able to realise shapes in the future that would
only be feasible in conventional construction at great financial expense.
Custom-fit production for bath tub and shower trays
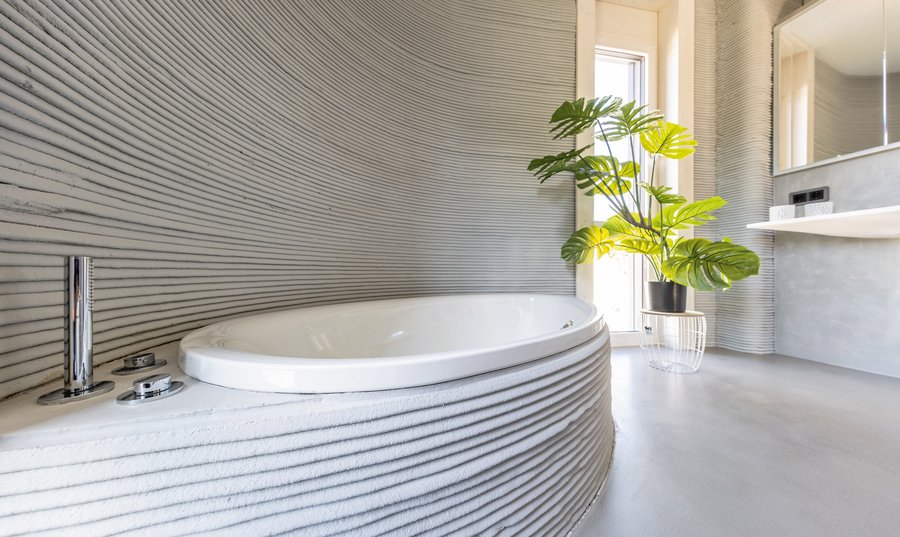
The BettePool Oval fitted perfectly into the design of
the rounded house wall and the bath apron.
Photo: Peri GmbH
The
two-storey residential building in Beckum with around 160 square metres of
living space was first created three-dimensionally on the computer before the
3D concrete printer printed everything out with centimetre precision. And that
was done in the course of just a few days. At a speed of up to one metre per
second, the print head spit concrete out like cream from a squirt bag while it
moved along its programmed path on a permanently installed metal framework.
Layer by layer, the walls of a building grew upwards. An exciting moment for
architects and craftsmen was the insertion of the bath products into the
printed form. But not only did the installation of the two BetteFloor shower
surfaces into the prefabricated components go smoothly, as architect Alexander
Hoffmann mentions, the BettePool Oval also fitted perfectly into the design of
the rounded house wall and the bath apron, which had also been printed from
concrete. An experiment that shows that it is possible that architecture from
the printer can successfully combine well thought-out design and high-quality
material with precise technology and modern methods.
Changing planning and construction process with 3D printing
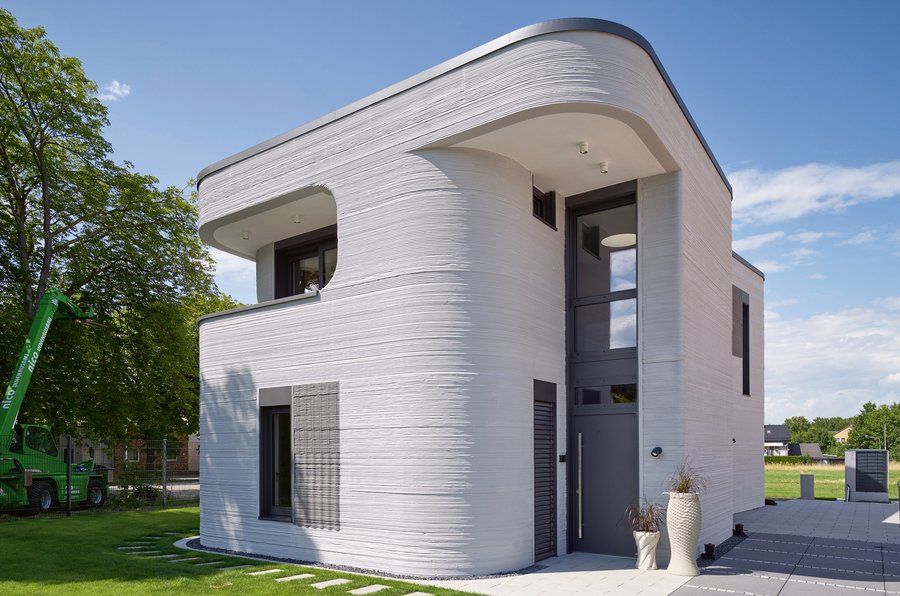
3D technology might change the planning and construction process of houses. This can be seen, for example, in the rounded corners of the Beckum 3D house.
Photo: Peri GmbH
As
Alexander Hoffmann and plumber Tobias Leifhelm (Leifhelm & Pelkmann) both explain
3D technology might change the planning and construction process of houses. The
special feature of this 3D house, Hoffmann says, is that it has rounded corners
everywhere. “Such features are very demanding to implement in conventional
construction and cost a lot of time.” With 3D printing, he carries on, “we save
about 50 per cent of the time.” Another advantage, the architect counts on, is
“the design freedom for the architect and the client. Then there are the short
construction times. The material savings. I need less manpower on the
construction site, two to three people are enough. And the fact that we can
implement the ancillary trades at an early stage and thus achieve a high
planning quality.” This is particularly
evident in the bathroom.
“The
bathroom is a very demanding space. Many trades are involved there,” Tobias
Leifhelm explains. “If everyone is on board from the beginning, you also
achieve good results. That's exactly what the 3D printing process requires,
i.e. that you coordinate all technical and design-related issues with everyone
involved at an early stage so that everything fits and works in the end. The
result is then also much better. It's really great that you can be so creative.
That we can find individual solutions that are also economically justifiable.”
Alexander
Hoffmann emphasises once more the importance of the motivation of all those
involved in the project: “With a project like this, it is extremely important
to have motivated people involved. We are doing research and innovation here,
you have to get everyone around the table and think about how to solve a problem.
I sweated blood and water over the bath. We had previously received a 3D file
from Bette with the exact curvature of the bath, and we fed this data into our
planning tool. But the fact that the bathtub really did fit perfectly in the
end was of course simply super.”
A detailed interview with Alexander Hoffmann and Tobias Leifhelm you can find here.