Inside Keuco: The production of Edition 90 fittings
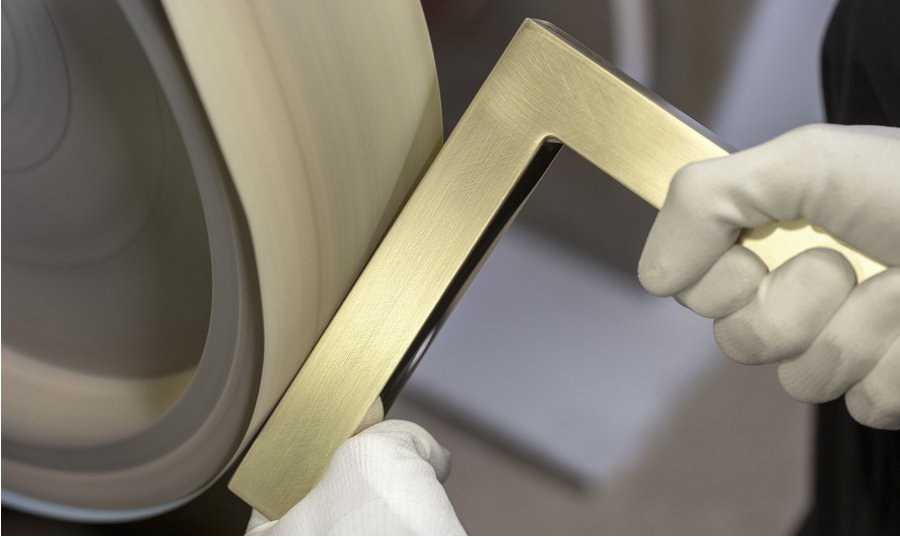
For the electroplating
process the fitting bodies need to be precisely grinded.
All photos: Keuco
More than 93% of all Keuco products
are produced in Germany. The basis for their products is the expertise of the Keuco domestic plants with their qualified employees. Using the example of the Edition 90 and a glimpse inside the product development and the production shows
what “Made in Germany” means to Keuco.
Design is always the first
point: Therefore Keuco collaborates with external design
agencies. The design of Edition 90 for example was developed together
with the design agency Tesseraux + Partner, Potsdam. A clear form language
embedded in a 90 degree angle is reflected throughout the complete Edition 90 bathroom furnishings range. A continuous design element of the
chrome plated fittings is the square on the round elements. Dominik Tesseraux
describes the development of new Keuco Products as “a process between the
designer, the Management, Head of Development, the Construction and the
Production.”
Circle meets square
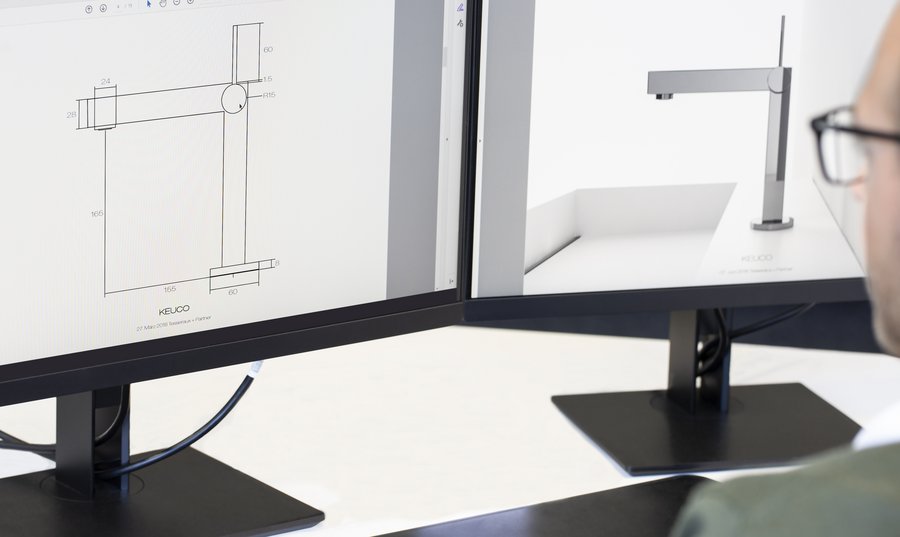
Circle and square are the visible, continuous design statement
throughout the Edition 90 fittings.
Hartmut Dalheimer, Managing Director of Keuco, reveals what is behind this: “The design idea is always the main focus
of the development process where Keuco products are concerned. It is a case of
exhausting the limits of production technology for the design idea. Our aim is
not only to make it possible from the technical point of view, but to make the
design technically possible. Only thus does this result in products which are unique
and enchant”. This is one of the reasons why Keuco also develop new
technologies.
Circle and square are the visible, continuous design statement
throughout the Edition 90 fittings which are characterized by
linear contours and shiny chrome surfaces. This is a real challenge for the
production because a precisely processed fitting body is inevitable for the
production steps where electroplating is concerned. Even the smallest
unevenness would be visible. Therefore it is crucial for the surface of the
fitting bodies to be 100% flat after the grinding and polishing process.
Innovative technology using fully automatic robots is used for this process, as
well as a manual fine-grinding step.
Processing in three stages
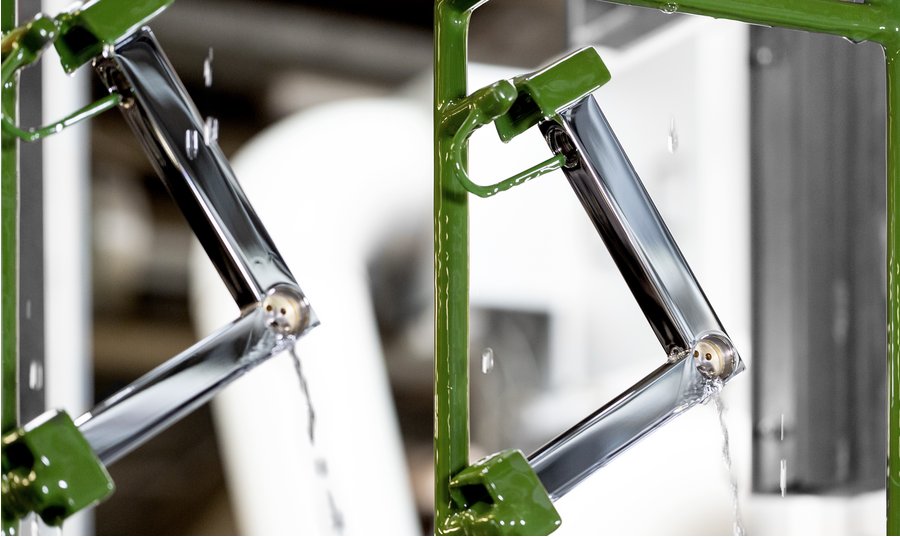
At Keuco, the surface finishing takes place in a three-stage process.
For Keuco the surface processing
is one of its core competencies.The brass fitting bodies are carefully
chrome plated with a high quality chrome coating in a special electroplating
process after the grinding and polishing process. The company has one of the most modern electroplating plants used in the sanitary
industry, where we achieve excellent chrome surfaces by means of a special,
three-stage process. The conventional method of producing a chrome surface
normally involves two stages: first of the all, the brass body is nickel-plated
and then chrome plated in a second step. Keuco has also integrated a semi-gloss nickel
stage in the process – for a particularly deep shine and corrosion protection
for many years.
And in the end: inspection
and tests – over and over again: Not only does every piece undergo a
visible quality inspection or is tested for functionality, or technical
material tests are carried out between the individual production steps, but
each piece is also inspected for quality during the final assembly stage.