Inside Dornbracht: Traditional craftsmanship and digital technology
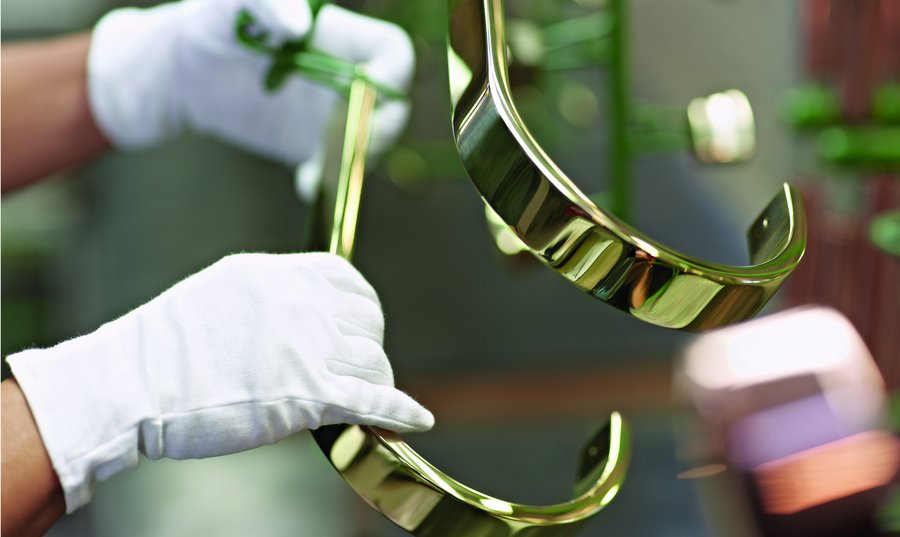
All photos: Dornbracht
Iserlohn is the largest city in the Sauerland
region (North Rhine-Westphalia, Germany) and has been shaped by metal
processing since the Middle Ages. The Dornbracht family
business is located here. Even in the age of technology
and digitalisation, the manufacturer of fittings continues to rely on manual
work in large parts of the production in line with a long-standing tradition -
but without losing sight of topics such as digitalisation in the area of conflict
between traditional craftsmanship and innovative technology.
High-tech and handcraft do not have to be incompatible opposites, they
can also complement each other sensibly.In
Iserlohn, all the production steps take place under one roof: from developing
new product solutions and programming relevant software, to electroplating, to
assembly. And even if the work in the factory is increasingly supported by
machines and industrial robots, the number of employees in production has
remained constant for many years. With good reason. Because every single
product passes through the hands of experienced skilled workers, who feel
almost personally responsible for “their” fitting – one of the most reliable
forms of quality assurance. And for the company it has always been one of the most reliable
forms of quality assurance.
Made in Germany – Made in Sauerland
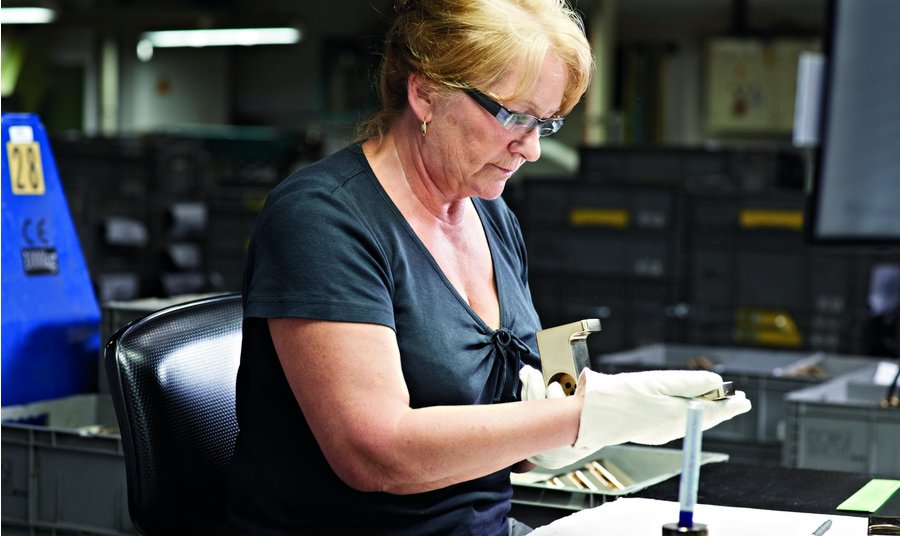
At Dornbracht, production means a lot of manual work in all areas and in almost every step of the manufacturing process.
“There can be no compromise in the premium segment, where we
do our business”, says Andreas Dornbracht, who is in charge of strategy,
finances, communication and marketing. This also applies to the label “Made in
Germany”, which is for Dornbracht both a statement of origin and a promise of
quality. The company not only manufactures in Germany, it also works almost
exclusively with suppliers local to Iserlohn – many of which are also
family companies with a long history. Stable business relationships with tried
and trusted partners from the Sauerland region, more than 60 years’
experience in the industry and the know-how of employees are one of the
cornerstones of the company‘s philosophy.
Therefore, not only highly specialised machines are used in production, it
is above all the knowledge of long-standing employees that counts - because
they have a lot of experience and a highly practised eye, of
course. Every single product is meticulously inspected and examined during its
production, with precision and professionalism. This means that a great deal of
manual work is brought to bear in almost every stage of manufacturing: in
finishing, grinding and polishing just as much as after the plating process, in
assembly – and in detailed checks after every step.
Quality before quantity
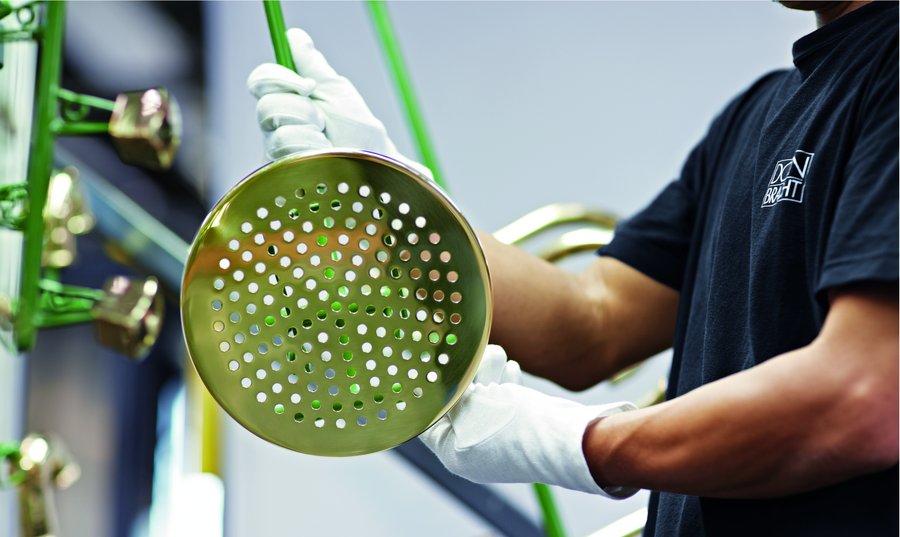
Dornbracht manufactures in Germany and works almost
exclusively with local suppliers.
To this day, relatively small quantities and even single pieces
are manufactured at Dornbracht, in response to individual
customer requests. “Neither a single radius nor a single edge will be changed
in our fittings for the sake of producing more items per unit time”, explains
Matthias Dornbracht, who is responsible in the company for developing systems
and technologies. Reaffirming the uncompromising standard we apply to
workmanship, functionality and design. Quality takes precedence over quantity -
and so there is no assembly line or piecework in the production halls
at Dornbracht.
For all the closeness to traditional craftsmanship Dornbracht
has long since moved into the digital age as well. The company presented it‘s
first digital product solutions for bathroom and kitchen in 2010, with the
Ambiance Tuning Technology (ATT). The digital portfolio was enhanced as early
as 2013, with the launch of Smart Water around the shower experienceSensory Sky ,
the electronically controlled Foot Bath and the intelligent kitchen
fitting eUnit Kitchen. In the second six months of 2019, the multi-sensory AquamoonATTshower
was launched onto the market – a response to the pursuit of holistic
well-being. Just tap the touch-screen to experience unique choreographies of
water, flow modes, mood lighting and fragrance. The control elements –
so-called Smart Tools – and the accompanying hardware and software are also
developed in the factory at Iserlohn.
Complementing not contradicting
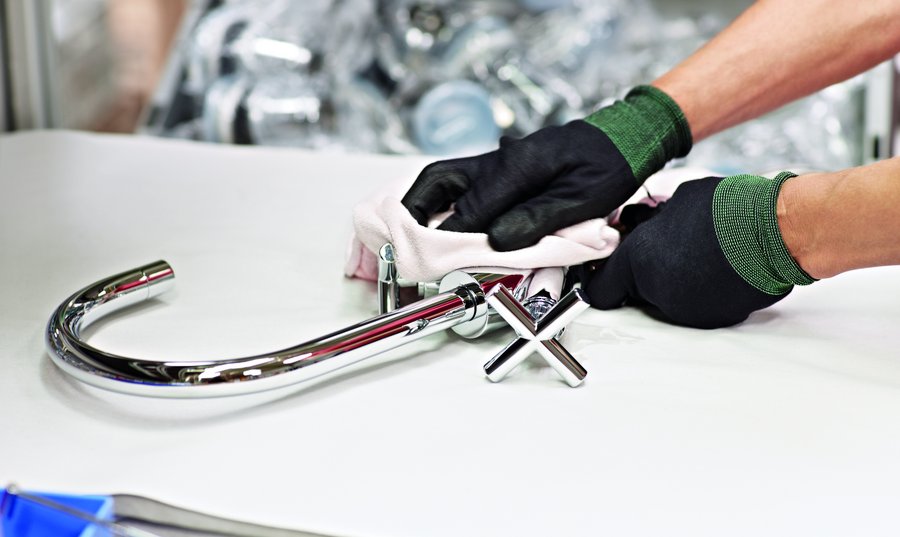
To this day, relatively small quantities and even single pieces
are manufactured at Dornbracht.
Andreas Dornbracht finds nothing contradictory about the
quality of manufacturing by hand and technological progress. “We are already
surrounded by digitality every single day. It is not a question of whether
high-tech and manual work can be compatible – they have to be. As leading
innovators in premium fittings, we have spent years dealing with the question
of how to reconcile traditional craftsmanship with technology – and in
particular additional digital value.” So the Smart Water technology is not
competing with fittings that are hand made, it represents their logical
development and completion. The equation is a simple one: Craftsmanship +
digital technology = fit for the future.
And the future means meeting the growing need for individualisation. For example, through digital solutions that can be used to select
personalised shower scenarios at the touch of a button. Manufacture
production also complies with the pursuit of individuality, as handmade
products are more likely to meet personal wants and needs than mass production.